steamquench.com - steamquench.org - steamquench.eu - steamquench.nl
Steamquench Optimizer®
Improvement of steam quench to mechanical seals of API Plan
62 pump systems, and reduce their overall maintenance costs.
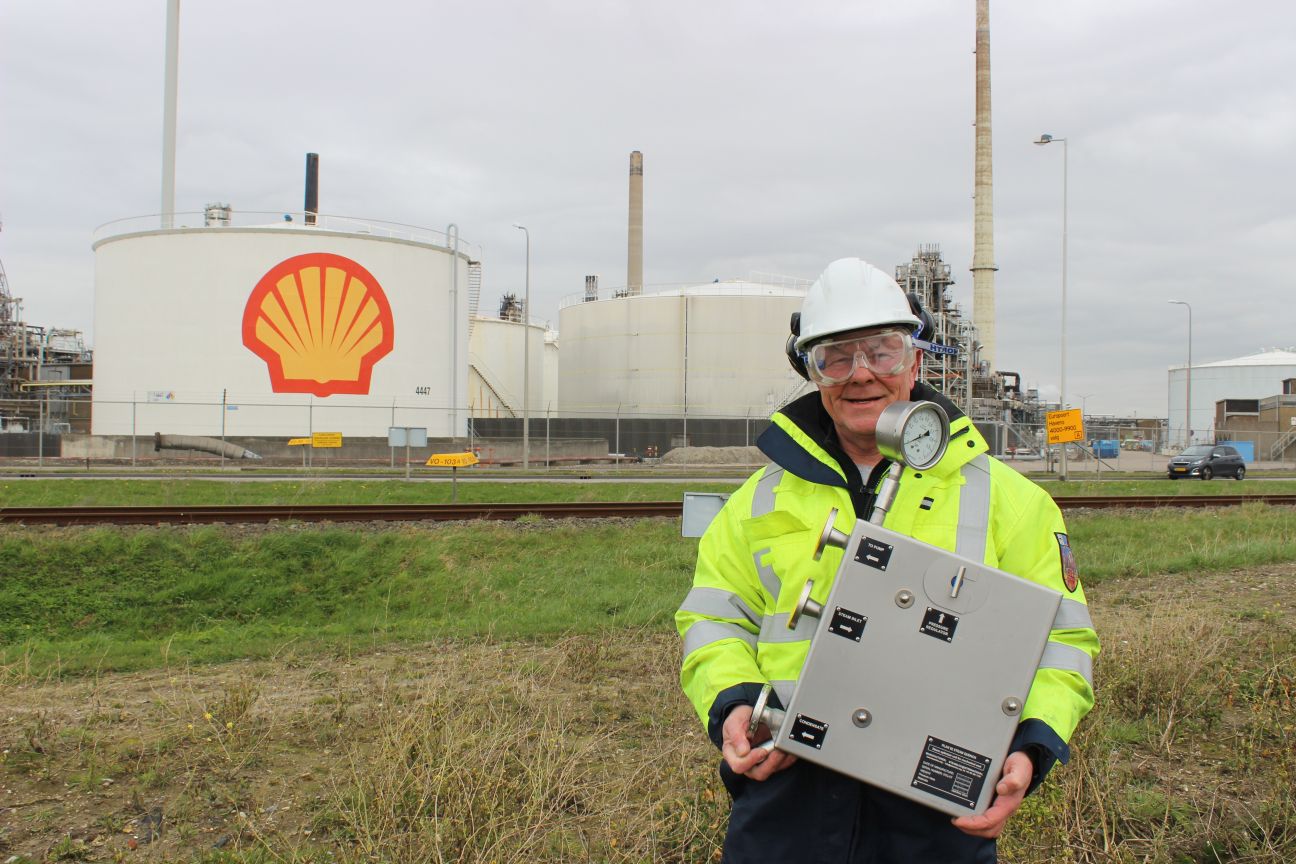
Incorrect line up, mistakes, and low maintenance priority on steam
quench configuration often cause seal damage after some time and
shortening the life of mechanical seals.
What are the underlying causes, and how to solve them?
In order to protect the mechanical seal of HT pump systems, refineries
use API plan 62 for selected pumps. Steam at ± 3 bar(g) or ± 45 psi(g)
feeds into a tubing system finally entering in the atmospheric side
of the seal at ± 0.2 bar(g) or 3 psi(g) to avoid entering air that
can cause coking.
This tubing system requires a separator, drip leg, needle valve,
and pressure gauge (fine scale) to control the feed of the steam.
These four functionalities are often installed as stand-alone devices
within the tubing system around API Plan 62 pumps.
Besides the fact that in some cases the separator is missing, such
a steamquench process is not always reliable due to manual handling
(e.g. separate position of devices, and irregular steam feed), with
a negative impact on the life of the mechanical seal.

To solve all these problem all at once, we developed the Steamquench
Optimizer
®,
integrating all four essential functionalities in one
‘plug & play’ cabinet or skid, once installed and fine-tuned, no
manual intervention required afterwards, making the steamquench
process more robust, and reliable!
By consequence the MTBR will be extended, which will reduce the
maintenance costs of these pump systems.
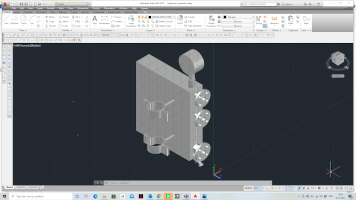
An isometric drawing is available for engineers.